How is Effective Microorganisms (EM) produced?
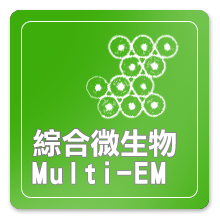
While the technical details on the production of Effective Microorganisms is part of the proprietary know-how for us, we can still share some light for you on the basic idea of the production procedures of GeoCare’s Effective Microorganisms product.
But we need to point out that this is the processes we go through, and may not be how other companies do it.
(1) Strain Selection: Purification of Effective Microorganisms (EM)
There are multiple strains of microorganisms inside the mixed cultures of Effective Microorganisms. Every single strain of microorganisms is selected from the nature environment where it is likely to be found to perform a certain function. Because we can found countless similar microorganisms in nature, we also need to go through a selection process to find out the most effective ones. If we want to form a workforce of microorganisms by duplicating them; of course we want to select the elites that have the best performance.
In some cases, the more extreme the condition is, we are more likely to find microorganism species that have stronger functionality. For example, if we want to find a microorganism that is effective in control a certain type of odor; we might need to go to the places where that kind of odor occurs severely. We then take samples of the microorganisms and select the best performing one out of them. This is the basic idea of how the microorganisms are selected. While the actual selection process is not as simple as it sounds. But the idea is that every single one of the strain in the Effective Microorganisms product is selected and purified individually before being mixed together by specific formulation.
(2) Formulation Design:
While every strain of microorganisms selected may have its specific performing area, we cannot simply put every strain we found into the mix. Not only we need to consider the production limitation (please refer to the following section on “Individual Fermentation”), we also need to consider the interaction between different species of microorganisms. Both anaerobic and aerobic microorganisms are selected and mixed; therefore, it is flexible for its application and utilization.
(3) Individual Fermentation:
Despite the fact that most of the microorganisms are produced through liquid fermentation process; we cannot simply put every one of them into the same fermentation tank and go through the sample fermentation condition and expect successful cultures to be produced. Because the characteristics and ideal condition for every microorganism is different, we need to culture each individual species in isolated condition to ensure they all reach target microbial count before mixing them together.?Due to the fact that we need to produce each microorganism separately to ensure proper development of each individual one, there is a limit as to the numbers of species that we can produce for a given product in a given production cycle.
(4) Centrifugal/Filtration Procedure:
In the liquid fermentation tank, microorganisms only take up a small portion of the liquid, and the rest are mostly water. In order to allow better efficiency during the drying procedure, we would use centrifuge or filter to remove most of the water content. And then these more concentrated liquid can be dried much more efficiently.
(5) Starch Powder Absorption:
Microorganisms itself is not visible and hard to preserve. Therefore, we use starch powders as the medium to carry these microorganisms. We use refined starch powder for GeoEM-B to make it easily water-soluble. We made this improvement based on the feedback from some users as they are used to application through irrigation system, and if the powder is too coarse; it might clogs the system.
(6) Drying & Mixing:
The starch with microorganisms is dried and mixed together. Low temperature drying process is performed to prevent the vitality of these microorganisms being affected. As mentioned before, every single microorganism is produced individually. We then mix these effective microorganisms together according to the proportion of our proprietary formula. ?Once the drying and mixing is completed, microorganisms are now in dormancy state and ready for packaging.
(7) Packaging:
Our effective microorganisms are packaged in sealed foil bags to prevent the microorganisms being directly exposed to sunlight. Nowadays the foil packaging usually comes as standard for most of the powder form products. This also marks another differences between liquid and powder form effective microorganisms since that most liquid effective microorganisms are bottle with plastic bottles that’s not completely opaque and may be more or less exposed to sunlight. In comparison, foil packaging is able to block most of the sunlight since it’s reflective and opaque.
(8) Storage:
Once packaging is completed, effective microorganisms are stored in the refrigerated warehouse under low temperature before being shipped out. Although refrigeration is not necessary as long as the storage location is cool, dry and not subject to direct sunlight, but refrigerated condition is even better. We do so to ensure the quality is not affected by exterior temperature.
(9) Shipping:
Most of the time, these effective microorganisms products can be shipped without refrigeration during transportation and still maintain its effectiveness as long as there is no exposure to severe high temperature for long period of time. Refrigerated containers are strongly recommended for long distance oversea shipments to prevent the heat from building up during the voyage. However, we have also shipped without refrigeration oversea as well, and the effective microorganisms still remain active after the shipment. This again demonstrates that powder form effective microorganisms is more suitable for storage and transportation while ensuring the quality of the product.